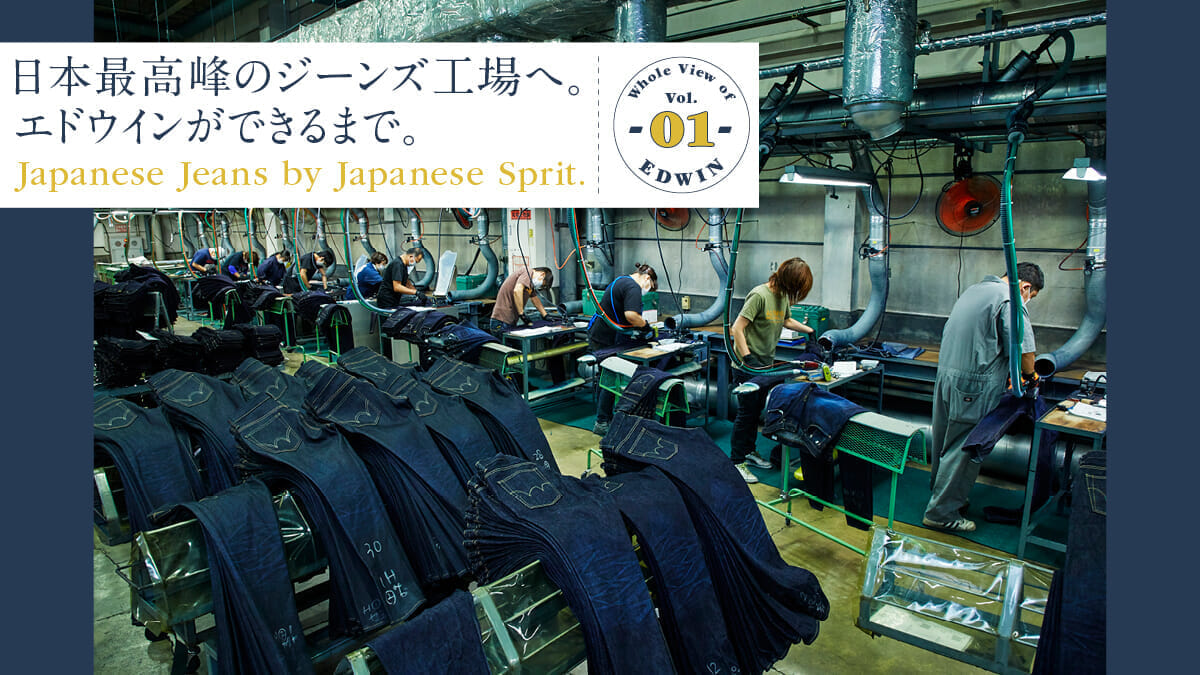
Japanese Jeans by Japanese Sprit.
日本最高峰のデニム工場へ。エドウインができるまで。Whole View of EDWIN Vol.01
日本のカジュアルファッション黎明期より、長年ジーンズをつくり続けてきた〈エドウイン〉。その長い歴史を、ものづくりという側面からしっかりと支えてきたのが、他でもないジーンズ工場と、そこで働く職人たちです。この企画では、日本最大のジーンズメーカーにまで成長した〈エドウイン〉の生産拠点である秋田県は縫製工場「秋田ホーセ」と、洗い加工工場「ジーンズMCD」を訪れ、一本のジーンズが出来上がるまでをレポート。〈エドウイン〉のものづくりに迫ります。
- Photo_Toyoaki Masuda
- Text_Tetsu Takasuka
- Edit_Yosuke Ishii